Neu am 20.11.2012
November 2011
Vor vielen Jahren sah ich auf einer Bootsausstellung Kajaks und Kanadier mit Holzgerüst und transparenter Haut. Sie waren superleicht und sahen unverschämt gut und elegant aus. Damals habe ich mich in diese Bauart verliebt. Sie nennt sich Skin on Frame (SOF) und lehnt sich an die Bauweise an die von Eskimos schon vor Jahrhunderten verwendet wurde. In USA und England (und anderen Ländern) gibt es offensichtlich eine richtige Bewegung, die sich ausschließlich mit solchen Booten befasst. In Deutschland gibt es inzwischen auch schon eine ganze Reihe solcher Boote, die von einigen Spezialisten und engagierten Amateuren gebaut wurden.
Bei uns in der Gegend, in Speyer, gibt es ebenfalls einen Bootsbauer, der solche schöne und leichte Eskimokajaks und Kanadier baut und den ich schon ab und zu im Otterstädter Altrhein paddeln sah. Natürlich musste ich diese Boote aus der Nähe sehen und durfte auch schon mal in der Werkstatt Bootsbau Dorsch alles im Detail betrachten.
Spätestens da wurde mir klar, dass ich mir nun endlich auch so ein Boot bauen muss.
Als erstes baute ich ein Modell im Maßstab 1:5 und stellte es mir ins Wohnzimmer um mich entsprechend einzustimmen. Nach einiger Zeit stellte ich fest, dass es mir doch nicht ganz so gut gefiel wie ich dachte.
Dann verbesserte ich die Form und baute ein neues Modell, das dann auch im Wohnzimmer stehen bleiben durfte.
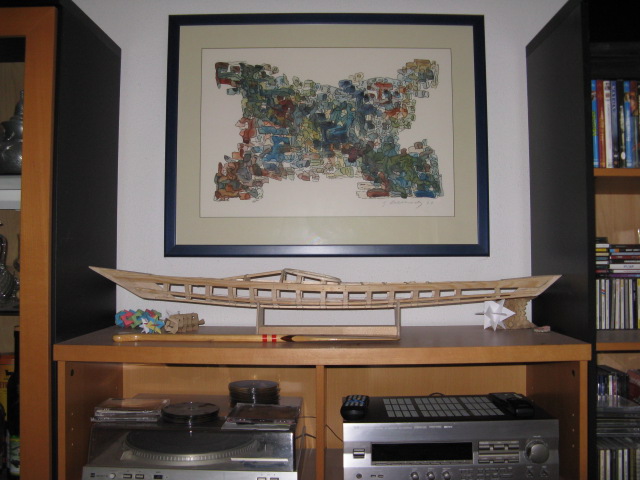
das „Wohnzimmermodell“
Nun begann eine sehr interessante Zeit in der bei mir das Internet glühte. Auf vielen englischsprachigen Seiten konnte ich mich mit meinen mickrigen Englischkenntnissen über die unterschiedlichen Bauweisen, Formen und Materialien informieren, bis ich mir über meinen eigenen Entwurf im klaren war. Besonders gut gefiel mir die Bauweise von Tom Yost, der statt der vielen dampfgebogenen Spanten eine überschaubare Anzahl von Sperrholzspanten verwendet. Das Kajak Sea Cruiser gefiel mir besonders gut und so änderte ich die Maße und Spantenzahl auf meine Bedürfnisse ab. Angepasst an meine Körpermaße wird es ein Kajak in angelehnter Westgrönländer Form mit ca. 540 cm Länge, ca. 57 cm Breite und -bedingt durch mein Kunstknie- einer Höhe von über 35 cm. Der Süllrand bekommt eine Innenlänge von 76 cm. Das angestrebte Gewicht soll unter 15 kg bleiben.
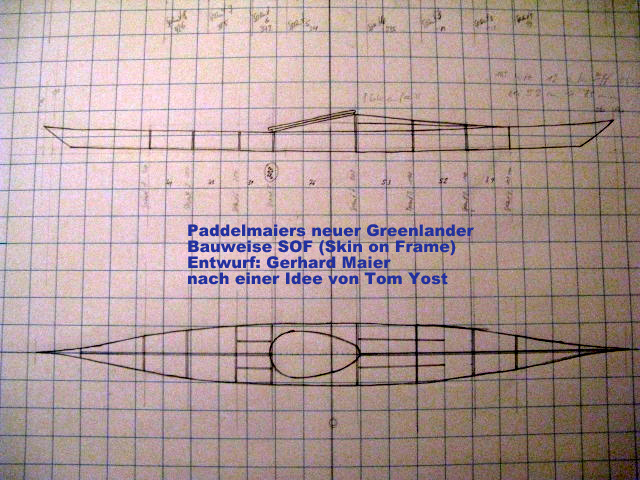
mein „Bauplan“
Nun ging es los mit dem berechnen und zeichnen der Spanten und der verschiedenen Leisten, denn das Kajak soll zwar leicht aber auch sehr stabil werden. Die Spanten werden also gewichtsoptimiert gestaltet und aus 9 mm dicken Birken-Multiplexplatten ausgesägt.
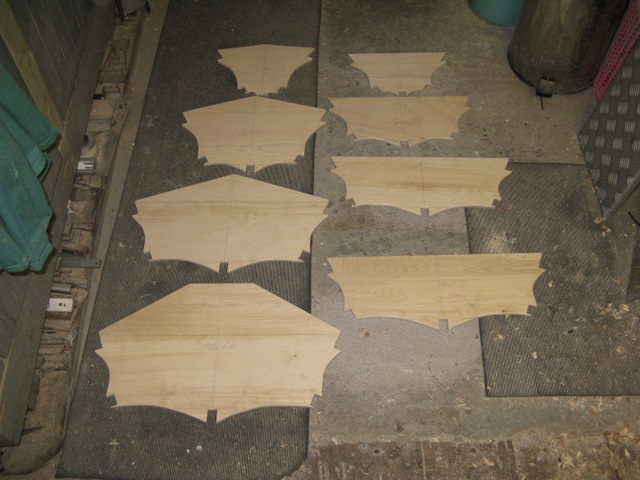
Die Spanten haben ihre Außenkontur
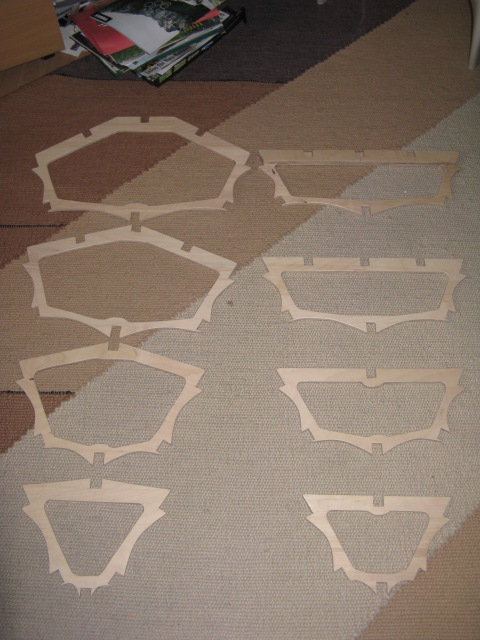
und so sehen sie fertig aus
Nachdem die Spanten fertig waren kam die nächste interessante Aufgabe, die Herstellung des Süllrandes aus mehreren Schichten von dampfgebogenen Kiefernleisten. Als erstes sägte ich eine Schablone aus Spanplatte aus, die die Innenkontur des Süllrandes hatte. 20 Bohrungen für die Klemmen und Schraubzwingen sollten ausreichen um die Leisten in Form zu bringen.
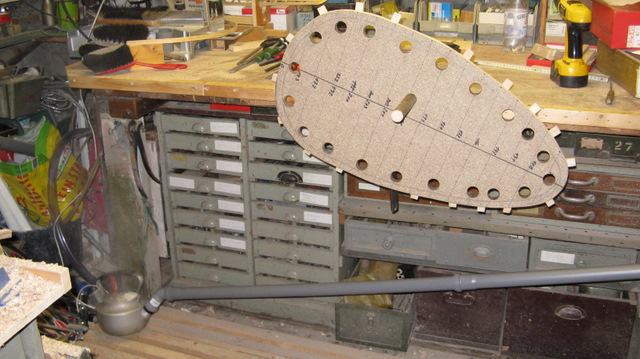
Biegeform für den Süllrand
Aus einem alten elektrischen Wasserkessel und 40 mm Kunststoffrohren baute ich mir ein “Dampfrohr” in dem ich die Kieferleisten ca. 1 Std. dem Dampf aussetzte und dann um die Form bog. Es war das erste Mal, dass ich Holz mit Dampfunterstützung gebogen habe, es ging leichter als erwartet. Die erste Lage wurde formverleimt, nachdem der wasserfeste Leim getrocknet war kam die 2. Lage dran. Wieder 1 Stunde Leiste im Dampfrohr, dann kam die 2. Runde auf die Form. Morgen wird dann diese 2. Lage mit der ersten formschlüssig verleimt, dann kann ich als nächstes den Süllrand, den Wulst für die Spritzdecke anfertigen. Der Süllrand sah zwar gut aus kam mir dann aber doch etwas zu fragil vor. Ich werde später also einen 2., stabileren herstellen.
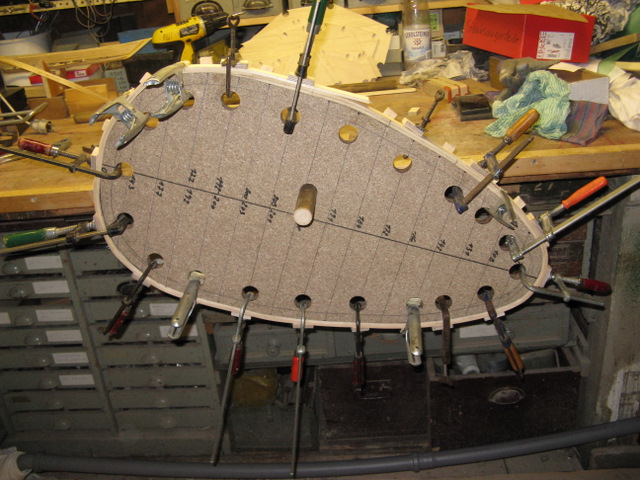
2 Lagen 5 mm Kiefernleiste sind gebogen
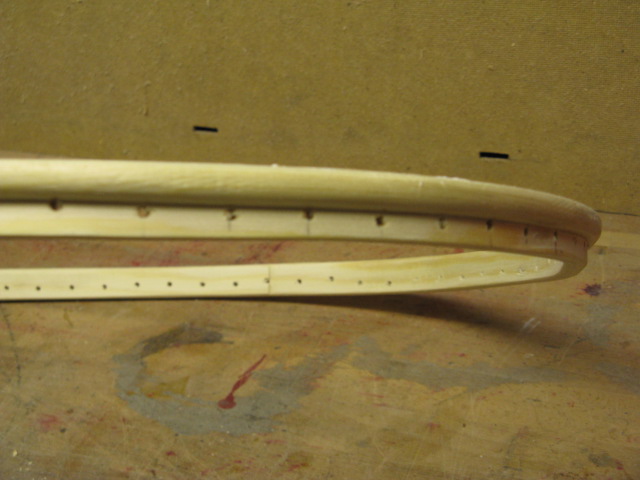
die Süllrandkontur ist durch eine 3. Lage fertiggestellt
Als nächste Arbeiten kommen nun die Bug- und Hecksteven dran, dann muss ich die Leisten für das Gerüst anfertigen.
Da ich diese Arbeiten nicht mehr im Keller durchführen kann muss ich wohl auf angenehme Temperaturen warten um im Freien oder im kalten Bootshaus arbeiten zu können.
Februar 2012
Die nächsten Arbeiten fanden dann in unserem Bootshaus statt. Zuerst mussten alle Längsleisten angeschäftet werden, da meine zurechtgesägten Leisten nur ca. 2,70 m lang waren. Das Kajak sollte aber ca. 5,4 m lang werden.
Danach wurden die mittleren Spanten mit den oberen Längsleisten, den Gunwales verschnürt, die Bug- und Hecksteven, die ich aus 9mm Birken-Multiplex ausgesägt hatte, angepasst und die Kielleiste mit Spanten und Steven verschnürt. Es folgten die weiteren Spanten, so dass die Form des Kajaks bald zu sehen war. Das Deck hinter der Sitzluke wird durch verschiedene Längsleisten stabilisiert, so dass man beim Einsteigen darauf sitzen kann. Das Vorschiff wird im Süllrandbereich stark hochgezogen so dass ich genügend Platz für meine lädierten Knie habe.
Wie vorhin schon beschrieben werden alle Verbindungen zwischen Spanten und Leisten mit künstlichen und sehr reißfesten Sehnen verbunden, es wird nichts geschraubt, genagelt oder geleimt. Nur die beiden Steven werden mit den oberen und unteren Längsleisten mit Holzdübeln fixiert.
Leider hatte ich bei diesen Arbeiten vergessen zu fotografieren, so dass nachfolgend nur Bilder des fast fertigen Gestells zu sehen sind.
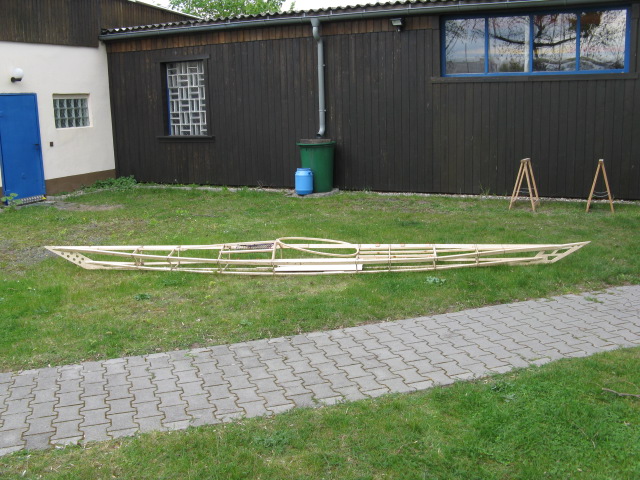
das Gestell ist fast fertig
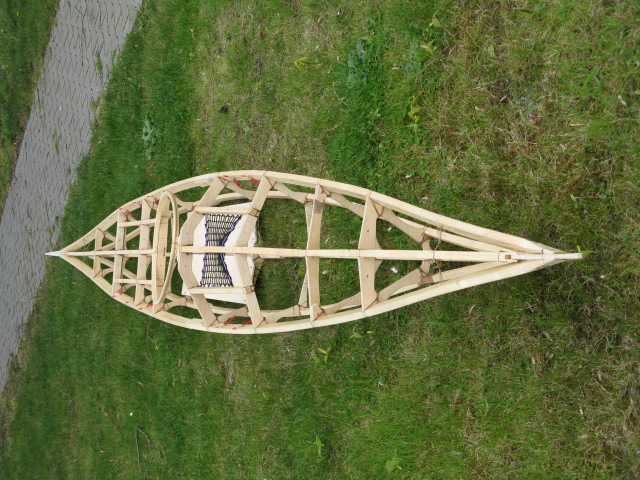
Blick von oben
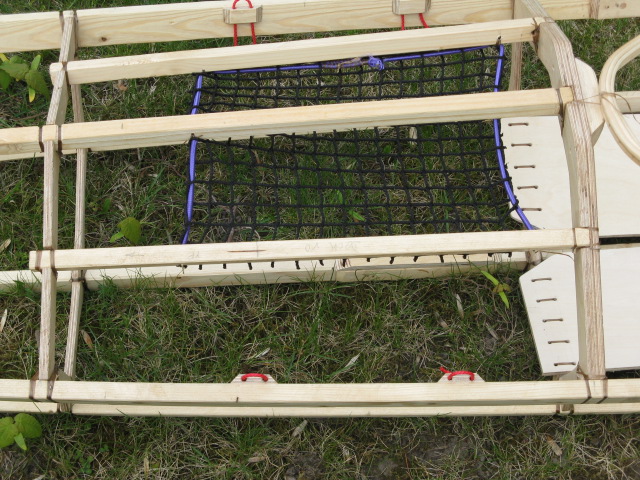
das Gepäcknetz ist bereits eingebaut
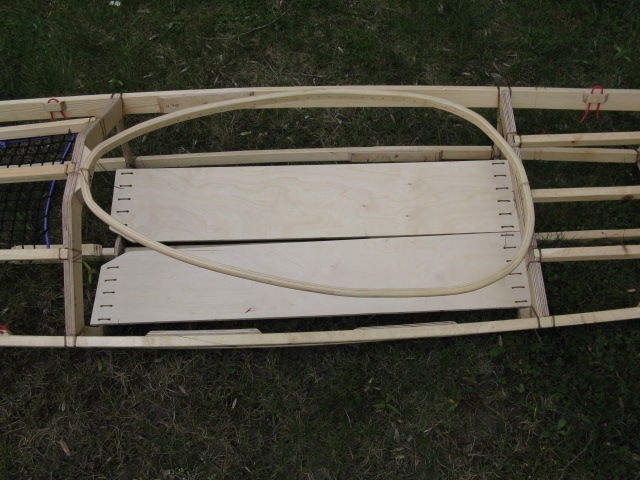
die Bodenplatten für den Sitz sind eingenäht
Ende Februar stand dann eine kleine Operation an der linken Hand an.Normalerweise ist man dann in 2-3 Wochen wieder handlungsfähig. Leider hatte ich das Pech, dass sich bei der OP Bakterien in der Wunde eingenistet haben und ich dadurch bis Ende Juni nicht mehr am Boot arbeiten konnte. inzwischen habe ich 2 weitere OPs hinter mir und die Hand ist wieder ziemlich ok.
Interessant ist für mich auch die Entwicklung, die man selbst durchmacht bei dieser ganzen Bastelarbeit. Man entdeckt beim Arbeiten immer wieder, dass es bessere Lösungen gibt, bleibt aber meistens dann doch bei der geplanten Bauweise. Wenn ich das Kajak nochmals bauen wollte würde ich z.B. nur noch 6 Spanten statt 8 verwenden. Die Querschnitte der Leisten würde ich auch verändern und die Bug- und Heckpartie weiter nach oben ziehen. Aber jetzt will ich erst einmal wissen wie die Näherei funktioniert, vielleicht wage ich mich dann doch noch an ein Nachfolgerboot.
Ende Juni 2012
Inzwischen habe ich auch schon ein bisschen Erfahrung mit dem Dampfbiegen. Der Versuch, den stabileren Süllrand aus 10 mm starken Leisten zu biegen ging schief. An der starken Rundung des vorderen Süllrands brach die Leiste, vielleicht war sie nicht lange genug gekocht oder die Maserung der Kieferleiste nicht gut genug. Mit 5mm starken Leisten hatte ich dann kein Problem. Der Süllrand entstand aus 2 St. 30x5mm und der Wulst ebenfalls aus 2 St. 10x5mm Kieferleisten. Nach dem Biegen wurden die Leisten mit wasserfestem Leim verleimt und mit einem Gurt auf die Schablone gespannt. Dann begann die Hobel- Feil- und Schleifarbeit um den Süllrand in Form zu bringen. Der Hals wurde im Abstand von 2 cm mit 98 Bohrungen durchbohrt, um den Süllrand mit der Deckshaut zu vernähen. Dann wurde er zum Schluss 3 fach mit Bootslack lackiert. Er wiegt genau 400 g.
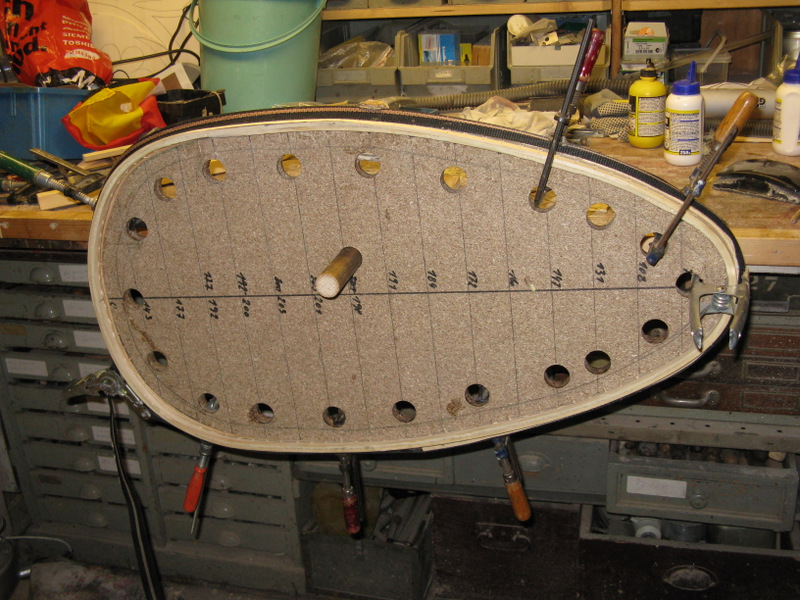
2. Versuch mit 5 x 30 mm Kiefernleisten um den Süllrand größer und stabiler zu gestalten
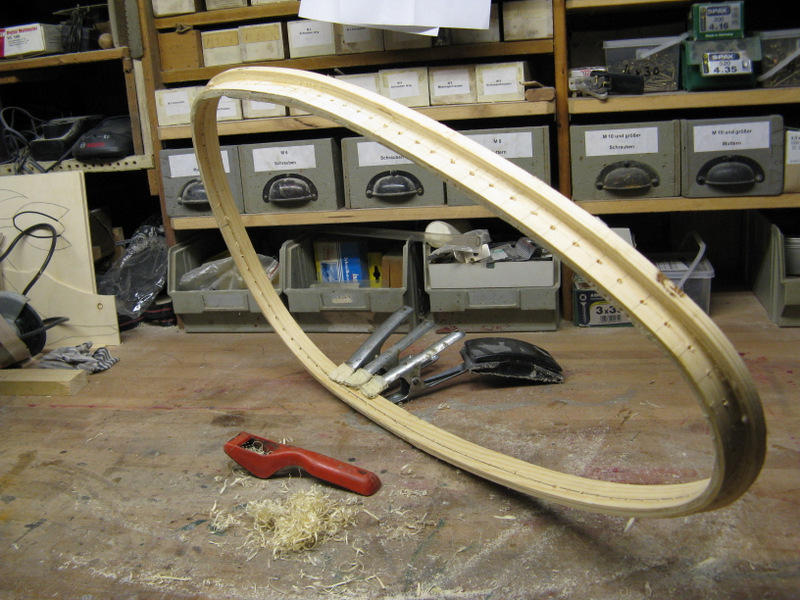
der Süllrand besteht aus 2 Lagen 5 x 30 mm und 2 Lagen 5 x 10 mm für den Wulst, hier noch im rohen Zustand
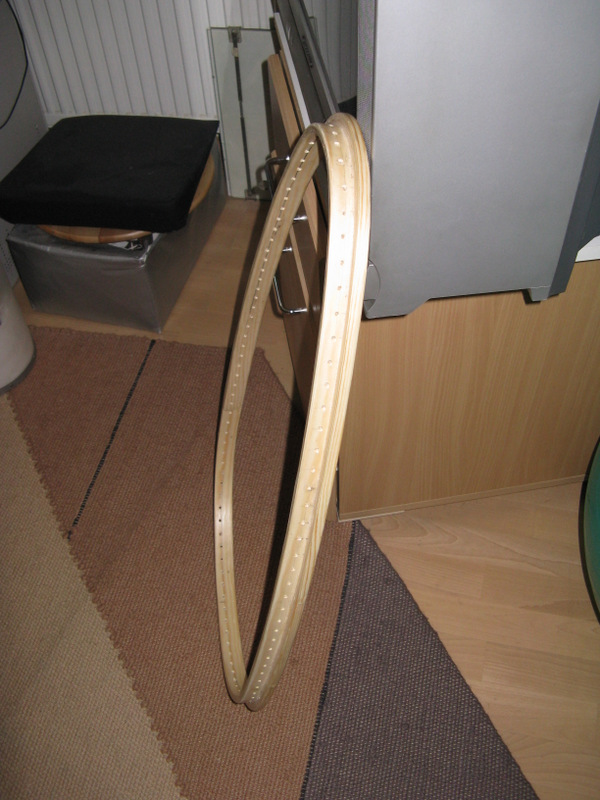
und so sieht er dann fertig aus
Im Juli kommt dann der interessante Teil, das beziehen des Gerüsts. Den entsprechenden Bezugsstoff -Ballistic-Nylon- konnte ich einem anderen Bootsbauer abkaufen, der genügend Material für mein Boot übrig hatte. Segelmachernadeln und Takelgarn hatte ich bereits besorgt und die erste Spitze ist schon eingenäht. Nun kommt die Hauptarbeit: 2. Spitze einnähen und dann den Bezug mit Gewalt über beide Spitzen ziehen. Danach wird die Haut unter Zug vernäht. Mal sehen, wie mir das gelingt.
21.07.2012
Heute geht es endlich weiter. Gerd, mein Sohn, kommt mit um das Gewebe mit aller Kraft in Längsrichtung zu dehnen. Ich habe 10 cm als Dehnung vorgegeben. Um das zu erreichen wird das Gerippe mit einem Gurt am Zaun festgebunden, dann können wir beide mit aller Kraft am Gewebe ziehen. Als die 10 cm erreicht sind, klemme ich den Bezug mit 2 Schraubzwingen und Holzleisten fest.
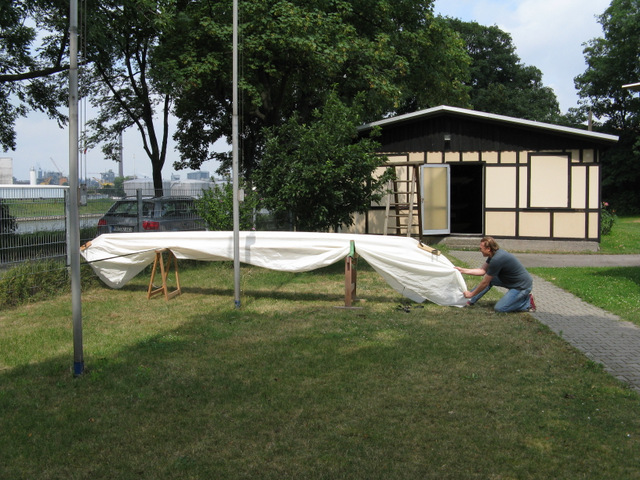
der Bezug wird mit viel Kraft über das festgezurrte Gestell gezogen und mit Schraubzwingen fixiert
Danach wird sofort die Spitze eingenäht damit sich der Bezug nicht mehr zurückziehen kann.
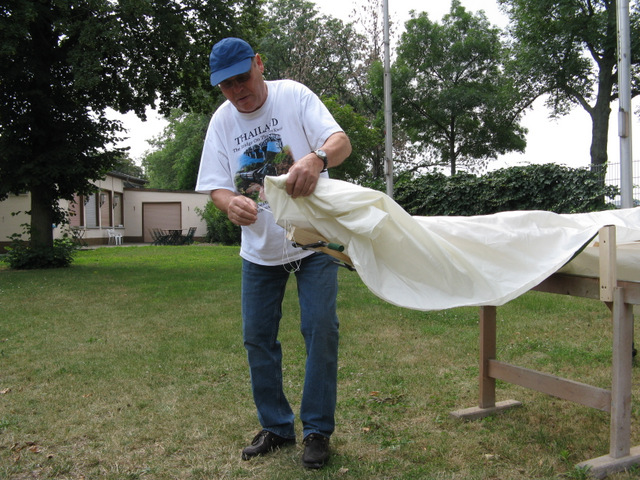
an der Spitze wird eine Tasche eingenäht
Als nächstes wird der Bezug mit Pinnwandnadeln auf der Kielleiste, danach auf den beiden Gunwales (Dollbords) fixiert.
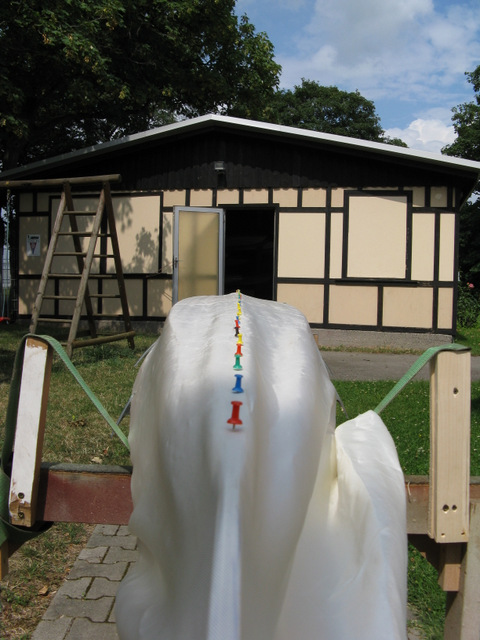
Fixierung des Gewebes auf der Kielleiste
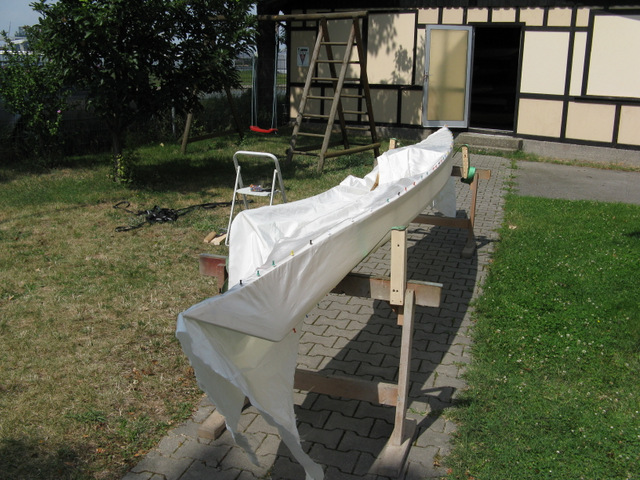
und an den Seiten
Nun kommt der Moment an dem genau überlegt werden muss, wieviel überflüssiges Material abgeschnitten werden darf. Ich lasse lieber etwas zuviel stehen, später kann man immer noch abschneiden.
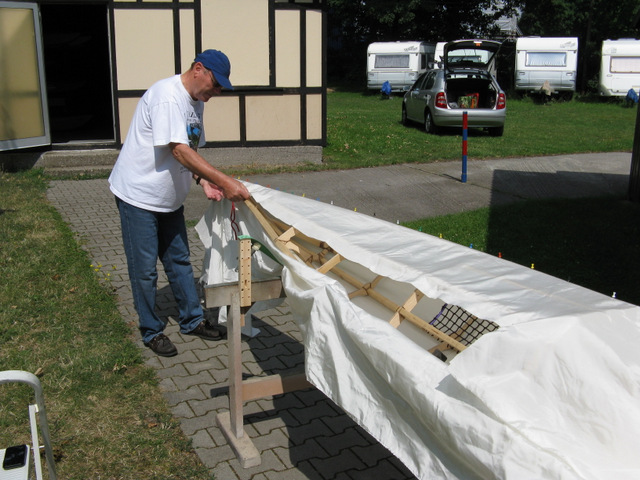
der erste Schnitt ist gemacht
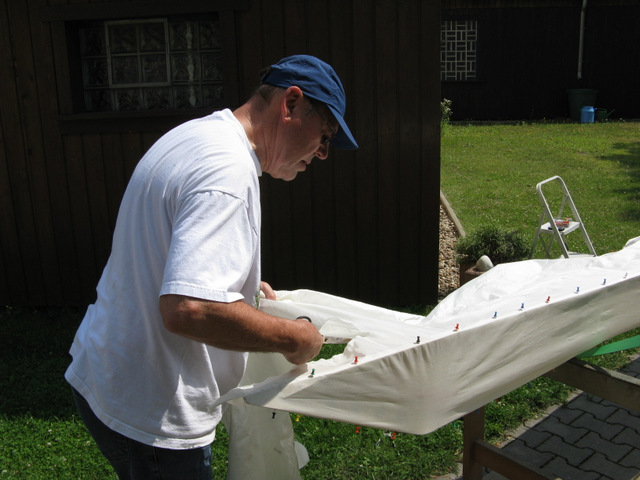
nun wird das restliche überschüssige Gewebe abgeschnitten
Der Bezug wird nun in der Mitte des Decks festgesteckt, so allmählich ist dann auch die Bootsform zu erkennen.
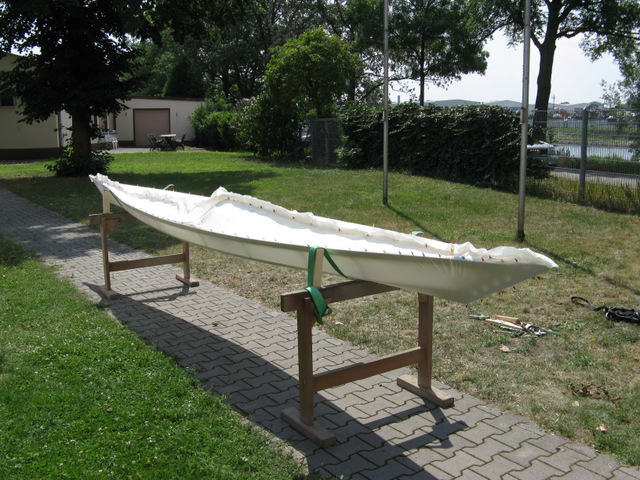
nachdem das Gewebe festgesteckt ist kann man sich schon die Bootsform vorstellen
Nachdem der Bezug fest auf dem Gerippe sitzt will ich natürlich auch wissen, wie das Boot mit Süllrand aussehen wird. Er wird in die richtige Lage gebracht und mit einem Gurt an den Rumpf gespannt, so dass er nach dem Nähen einen kräftigen Zug nach oben ausübt und so die Haut noch stärker spannt.
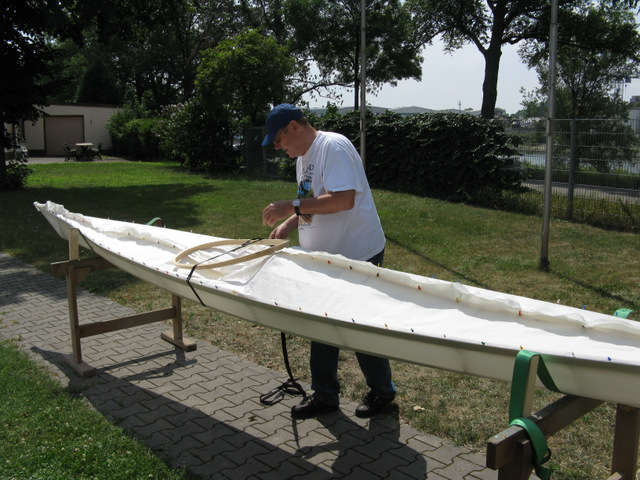
der Süllrand wird angeschnallt
So, für heute ist Arbeitsende, ein Gewitter zieht auf und es wird sicher nicht mehr lange dauern bis es regnet.
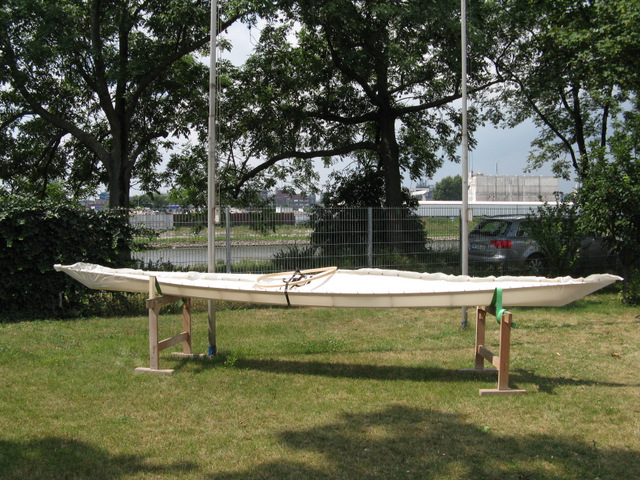
mir gefällt es schon jetzt
Wie vermutet, ging es dann ganz schnell. Kaum war das Boot in der Halle und das Werkzeug weggeräumt, ging ein Wolkenbruch los, der sich zum Gewitter steigerte.
Inzwischen liegt das Boot bei mir im Garten unter der Pergola und einem Pavillon, damit ich in Ruhe die Bespannung zusammennähen kann.
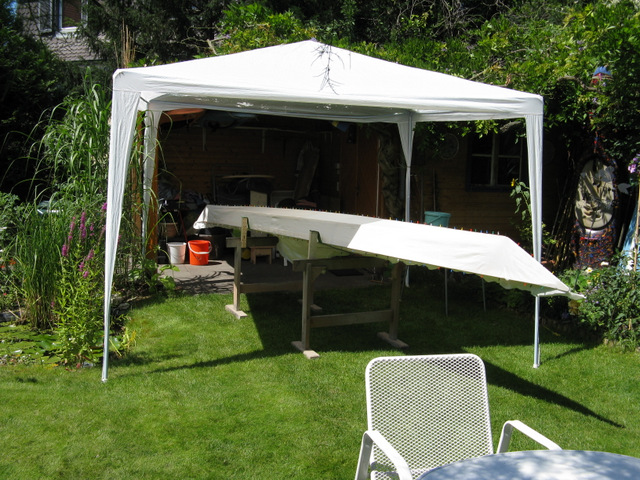
die Sonne brennt, daher lässt es sich unter dem Dach angenehmer arbeiten.
Zuerst wird das Bespannungsmaterial nochmals gespannt und mit Nadeln festgesteckt.
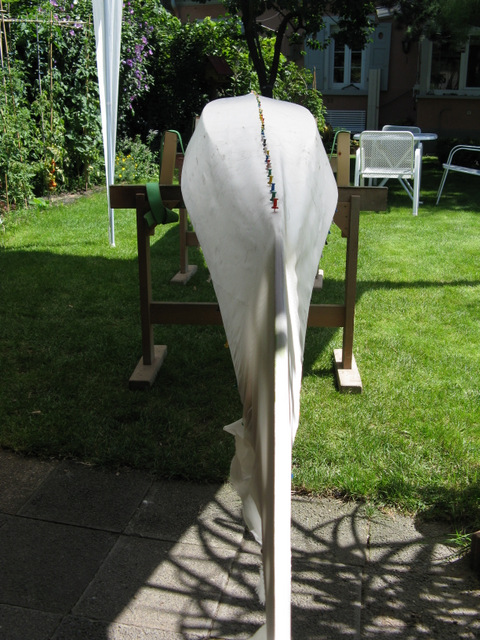
die Haut ist festgesteckt, nun kann das Nähen beginnen.
Unter Zug werden die beiden Seiten zusammengenäht und immer wieder nachgespannt.
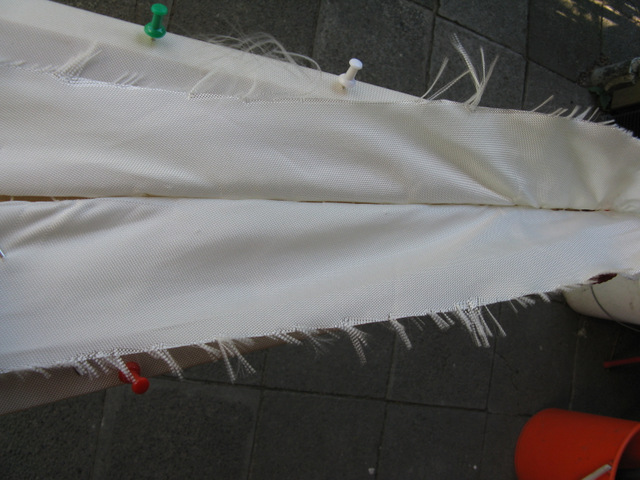
so sieht die erste Naht von oben aus
Es ist eine ziemlich mühsame Geschichte, wenn man zum ersten Mal so lange Nähte herstellen muss. aber irgendwann ist auch das geschafft und man kann zum nächsten Schritt weitergehen.
Der Süllrand wird aufgelegt und mit einem Gurt stark nach unten gespannt. Wenn dann der Süllrand eingenäht ist und der Gurt entfernt wird spannt der Süllrand die Bootshaut zusätzlich nach oben.
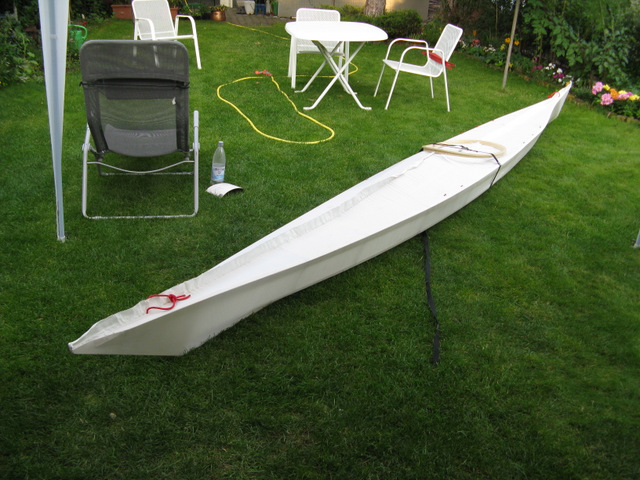
die Nähte sind fertiggestellt
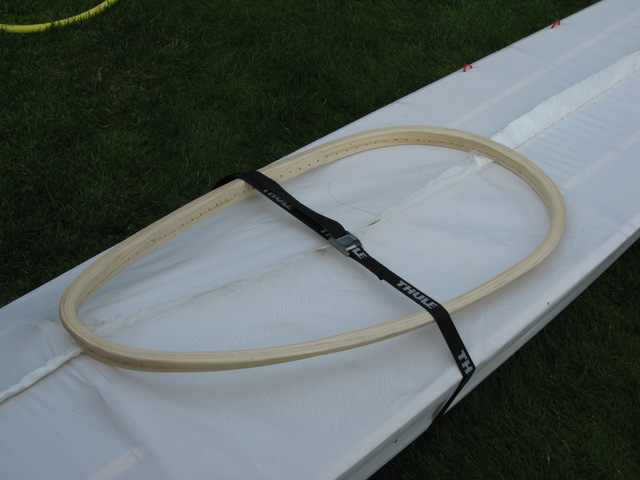
der Süllrand wird verspannt
25.07.2012
Nachdem der Süllrand fertig eingenäht ist kann der Gurt entfernt werden und das Boot liegt bereit zum ersten Probesitzen.
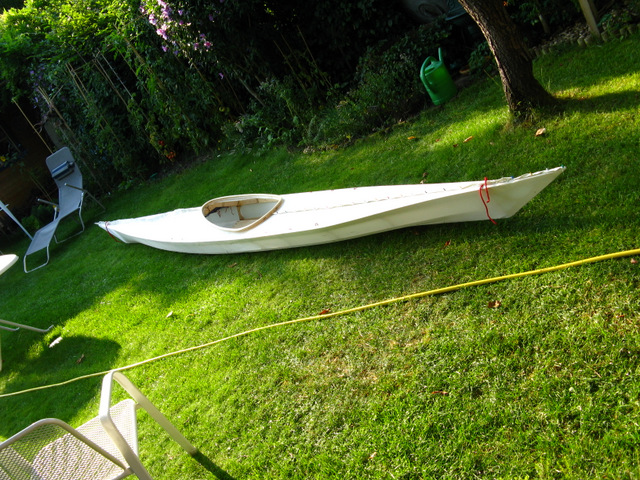
das Boot ist bereit zum Probesitzen
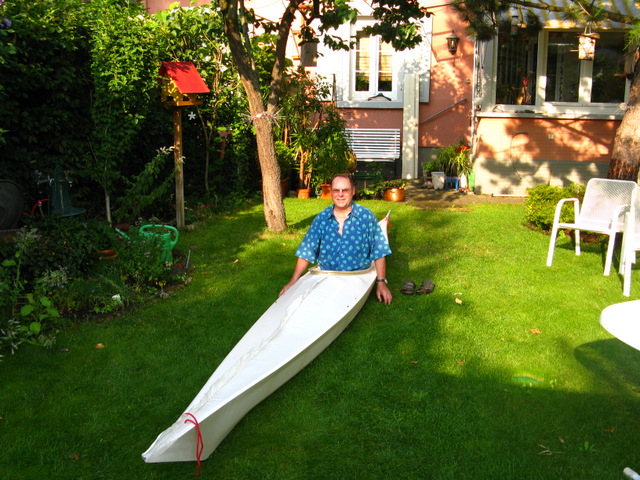
und wie man sieht, passt es wunderbar
Jetzt kommen die letzen Feinarbeiten an die Reihe. Die Überstände vom Zusammennähen werden zusammengelegt oder gerollt und mit dem Deck vernäht. Hier benötigt man eine Rundnadel und sollte versuchen eine möglichst gerade Linie einzuhalten. Schließlich muss man bei jeder Fahrt sein Werk betrachten.
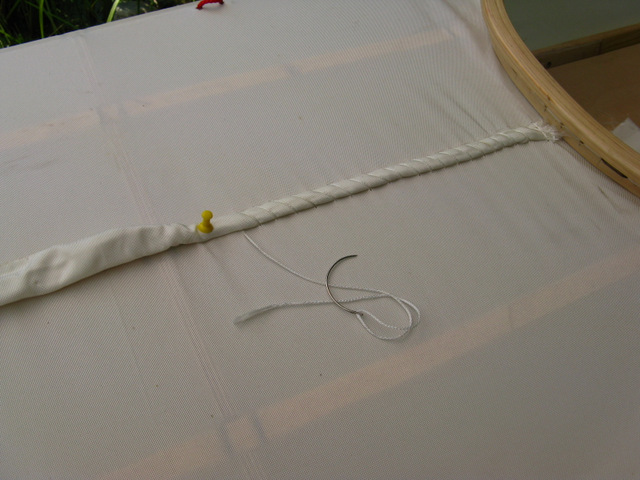
die Abschlussnaht erfordert nochmals viel Feingefühl.
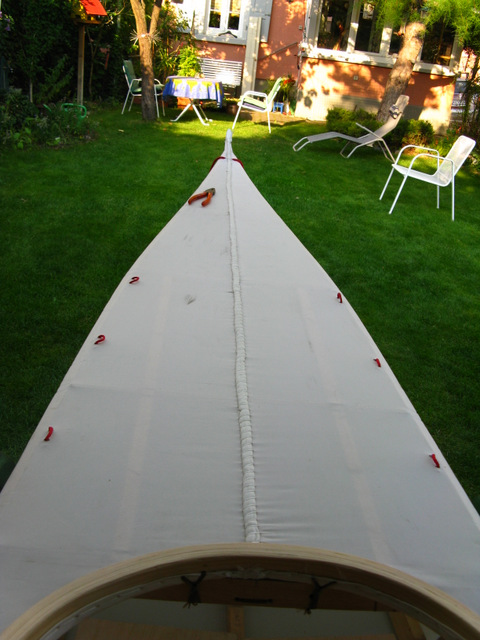
Die Naht des Hinterschiffs ist fertig, nun kommt das Vordeck an die Reihe
Das Boot ist nun aber leider noch nicht einsatzbereit. Die Haut muss noch gespannt werden, das geschieht durch Wärmezufuhr, z.B. beim Bügeln. da zieht sich das Material nochmals zusammen und wird straffer. Diesen Effekt konnte ich die letzten Tage beim Nähen beobachten, denn wir hatten die heißen Tage mit Temperaturen bis 36°C. Die Bootshaut war dann straff wie eine Trommel. Nachdem es gestern Nacht gewittert und heute mehrmals geregnet hat konnte man die Falten in der Bootshaut sehen, sie war deutlich schlaffer.
Nach dem Bügeln wird dann das gespannte Boot in mehreren Lagen mit Flüssig-PU beschichtet. Dadurch bleibt die Haut glatt und sehr elastisch.
Das PU-Material ist bestellt, ich nehme an, dass ich am Dienstag mit dem Beschichten anfangen kann.
26.07.2012
Das flüssige Pu (Coelan) ist da und ich gehe natürlich sofort an die Arbeit. Die Haut wird mit dem Bügeleisen bearbeitet um sie zu spannen und danach gehe ich noch mit dem Heißluftgebläse über das ganze Boot. Die Haut ist nun straff wie bei einer Trommel. Die erste Lage Coelan verdünne ich mit ca 25% Coelanverdünner und fange an das Unterschiff zu rollen. Insgesamt 3 Lagen streiche ich mit dem vorhandenen Material. Als es fest ist, was sehr schnell ging, wird noch das Deck des Kajaks gerollt. Dann ist allerdings das teure PU zu Ende und ich muss warten und eine neue Dose bestellen. Hier habe ich wohl etwas zu sparsam geplant.
06.08.2012
Inzwischen habe ich die neue Dose Coelan bekommen. Natürlich will ich das Boot so bald wie möglich fertig haben, also streiche ich das Deck noch 2 mal unverdünnt. Danach kommen nochmals die Seiten dran und wenn das alles trocken ist wird noch einmal der Boden gestrichen.
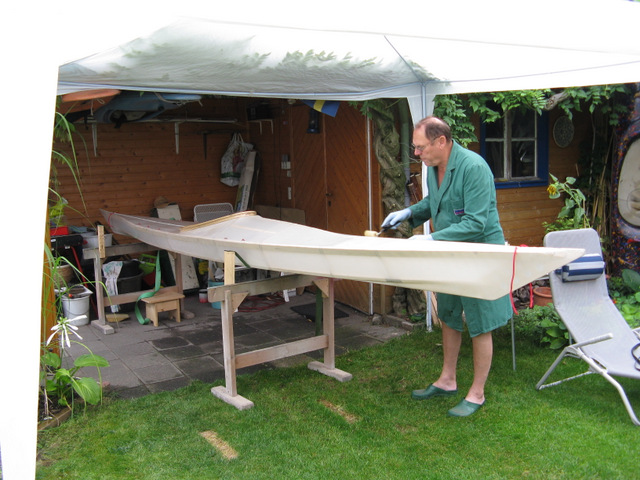
das ganze Boot wird mehrmals mit flüssigem PU beschichtet
Dann wird die Beschriftung und der Seitenstreifen aufgeklebt, die Decksbespannung eingefädelt und die Toggels zum Tragen angebracht.
11.08.2012
Und so sieht mein neues Kajak nun endgültig aus:
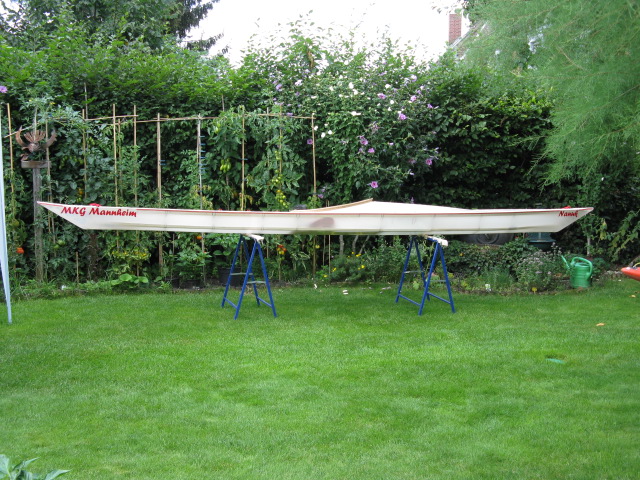
„Nanuk“ ist fertig
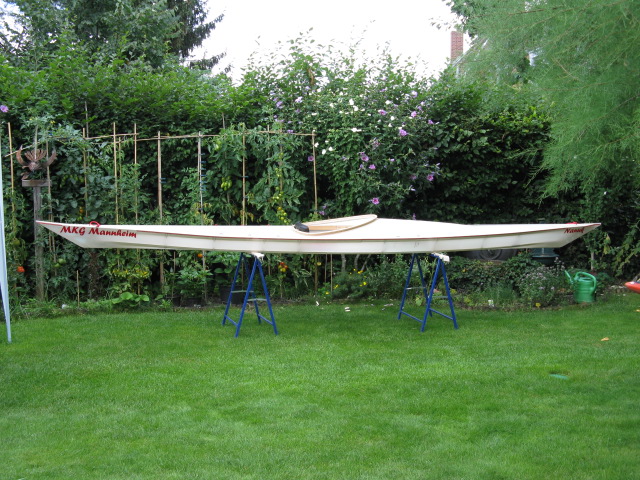
und wartet auf die Taufe und die erste Fahrt
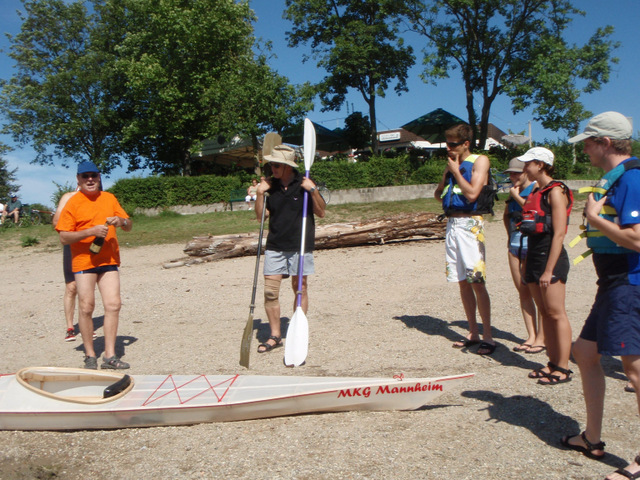
Bootstaufe am Otterstädter Altrhein
Die erste Fahrt verlief gut. Durch die rel. hohe Sitzposition kam mir das Boot etwas kippliger vor als gedacht. Außerdem hatte ich keinen Seitenhalt. Ich habe daher nochmals die Sitzgelegenheit verändert und etwas tiefer gelegt. Außerdem habe ich nun Seitenteile am Sitz eingebaut und habe dadurch eine sehr gute Fixierung im Sitz. Wenn es wieder richtig warm ist freue ich mich schon aufs eskimotieren.
Die nächste und vorläufig letzte Fahrt war Anfang Oktober auf dem Neckar bei Eberbach. Das Boot läuft super und es macht richtig Spaß in einem leichten Boot zu fahren. Mein PE-Seekajak wiegt bei fast gleichen Maßen doppelt so viel!
Nun noch ein paar technische Daten:
Bootslänge: 550 cm, Breite: 57 cm, Gewicht fahrfertig: 15,0 kg
ENDE der Geschichte